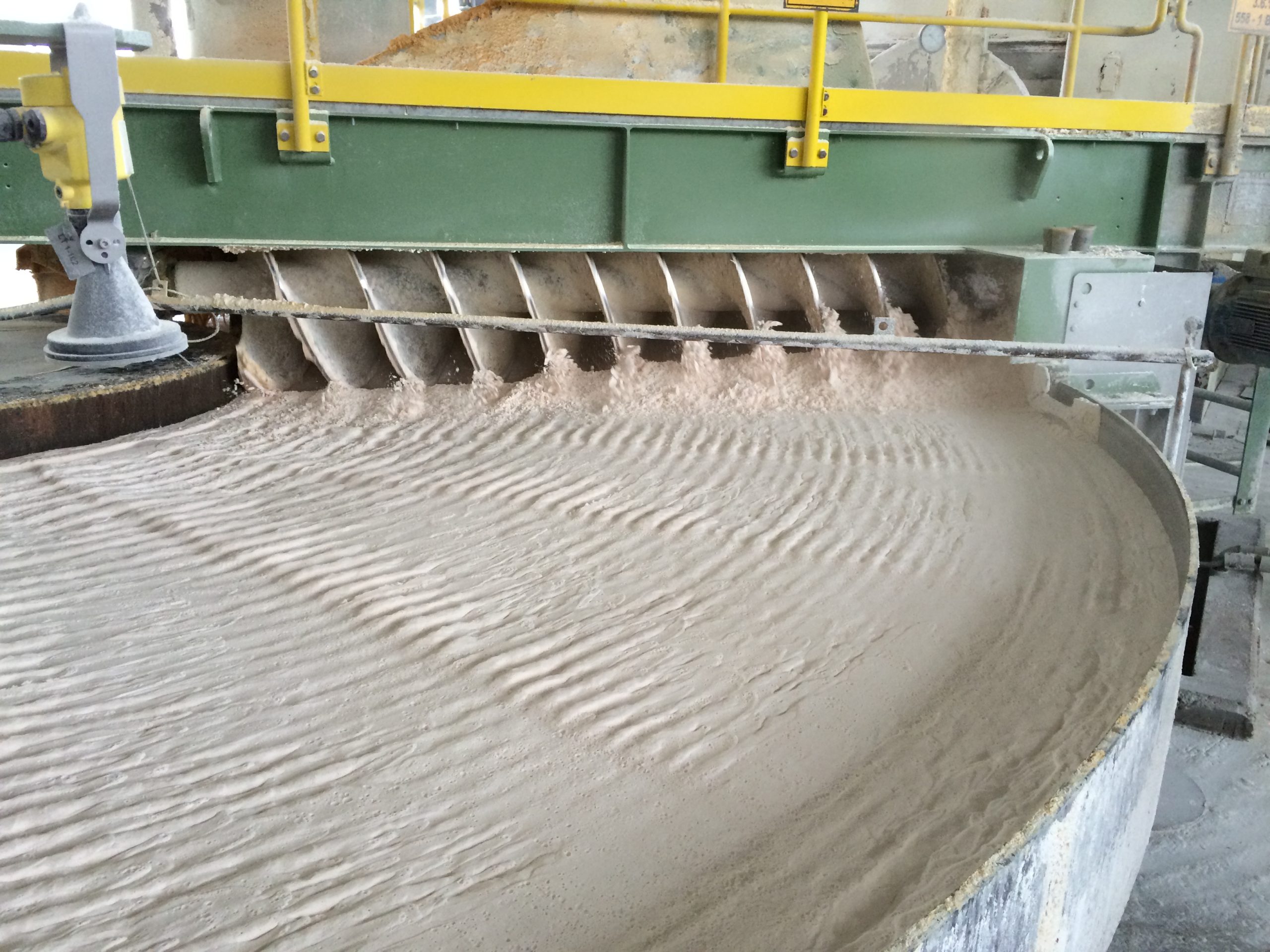
Chemicals
The chemical industry has a broad spectrum of applications and needs highly efficient and economic liquid-solid separation solutions. Leading chemical producers are interested in product purity, high yield, low operating cost as well as waste minimization to meet sustainability goals.
In addition to our woven fabrics, we offer hardware spares such as filter press plates, membranes and disc elements.
Agrochemicals
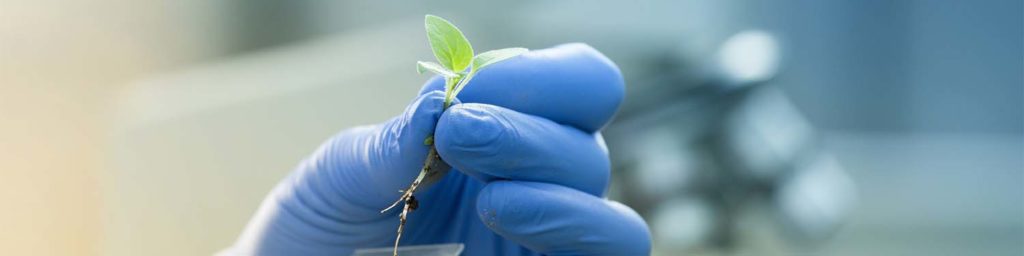
- Phosphoric acid
- Potash
The most commonly used filters are horizontal vacuum belt filters and rotary pan filters. Clear Edge understands all aspects of your production and our offerings are a result of collaborative efforts with equipment manufacturers and our daily work in the field with our customers.
Clear Edge’s range of filter fabrics for agrochemical products is woven in our ISO accredited facilities and has been compiled with the rigours of these processing plants in mind. Whilst parameters such as fabric weight, permeability, weave pattern and yarn type vary to optimise the filtration performance, our filter media is always crafted to be as robust and easy to install.